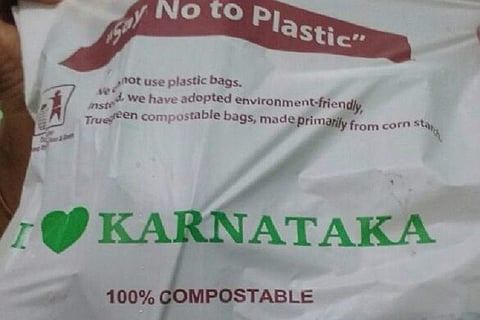
Synthetic plastics are a major source of pollution today. They are toxic, harm the environment, depend on fossil fuels and are non-biodegradable.
Scientists across the world have been working on developing technologies to create biodegradable materials that can replace synthetic plastic. Here are five eco-friendly alternatives to the polluting plastic:
Corn starch:
Also known as bioplastics, it is made from the resins extracted from corn starch. They last longer and are 30 percent stronger than existing polythene bags.
They look and feel like synthetic plastic, but are biodegradable. They can decompose in soil or garbage and break down within a few months or even weeks.
"The corn starch molecules they contain slowly absorb water and swell up, causing them to break apart into small fragments that bacteria can digest more readily," an explainthatstuff.com report states.
Chicken feathers:
Studies have found that chicken feathers can be used to make biodegradable plastic.
Chicken feathers are rich in keratin, a fibrous protein, and thus offer great strength and are tear-resistant. Additionally, the manufacture of such plastic does not depend on the use of fossil fuels.
Image for representation
The feather-based plastic can be used to make everything from carry bags to containers and even furniture.
Also, chicken feathers are available in abundance in several countries as they are often dumped as waste.
Plastic that dissolves in sea water:
This could be an answer to reducing the amount of plastic that ends up in our water bodies. When this plastic comes in contact with seawater, it dissolves within 20 days. It is also denser than salt water and so can help in preventing plastic from washing up on and polluting shores.
According to a 2007 report in LiveScience, researchers were working on plastics that "degrade in seawater".
Image for representation
Researcher Robson Storey, who is also a polymer scientist at University of Southern Mississippi, explained to LiveScience that this kind of plastic is "made of polyurethane modified to incorporate a biodegradable compound known as PLGA, which is used in medical sutures."
After they dissolve, "our goal is for them to break down into carbon dioxide and water," Storey added.
Milk protein:
Casein, a milk protein, is being used to develop biodegradable plastic films and could be in the market in three years. It gets better: it’s edible.
"These casein-based films are up to 500 times better than plastics at keeping oxygen away from food and, because they are derived from milk, are biodegradable, sustainable and edible," a report on Lancaster Farming states.
Image for representation
Some varieties of edible packaging available in the market are made of starch, which makes them porous and allows oxygen to enter through its microholes. However, casein-based ones have smaller pores which can keep the oxygen out, the report adds.
The technology can also be used to coat food directly, like cereals which at present are coated by sugar to maintain their crunch when milk is added to it. The casein-protein coating can prevent food from becoming soggy.
"Everything is in smaller and smaller packaging, which is great for grabbing for lunch, for school, but then it generates so much waste. Edible packaging can be great for that," Laetitia Bonnaillie, who co-led the casein packaging research, told Bloomberg.
Arboform or Liquid wood:
Products made of Arboform are already being used in durable products such as car parts, but it isn’t used to make household items because of the high sulphur content, DW reported. However, the Fraunhofer Institute for Chemical Technology (ICT) in Pfinztal, Germany, has developed a method that reduces sulphur content in Arborform by nearly 90 per cent, making it safer to use it to manufacture household products too.
"The cellulose industry separates wood into its three main components -- lignin, cellulose and hemicellulose," Emilia Regina Inone-Kauffmann, team leader, Fraunhofer Institute for Chemical Technology (ICT) in Pfinztal, Germany, told DPA news agency.
Image for representation
"The lignin is not needed in papermaking, however. Our colleagues mix that lignin with fine natural fibers made of wood, hemp or flax and natural additives such as wax. From this, they produce plastic granulate that can be melted and injection-moulded."